We've touched upon thread whirling in the newsletter before. Typically this has been done to introduce new higher helix whirling cutters. What we have not done is provide an in depth explanation of what thread whirling is, how it works, and the relative advantages it offers over other threading techniques.
Having realized our negligence, we offer the following piece as a primer on the subject. Look for more information about whirling inserts, cutter bodies and the newest whirling technology in future issues of the newsletter.
Having realized our negligence, we offer the following piece as a primer on the subject. Look for more information about whirling inserts, cutter bodies and the newest whirling technology in future issues of the newsletter.
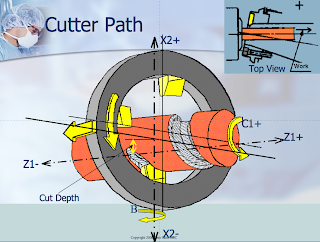
Reduced “pounding” on the cutter is a primary benefit of the whirling process as the cutting insert eases into and out of the cut, producing a comma shaped chip. The eccentric cutter path radius coincides with the work radius at the minor diameter, yielding very good roundness.
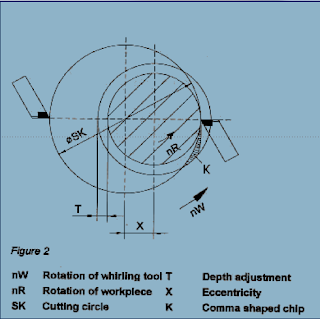
When compared to milling threads, whirling produces a number of the same benefits relative to cycle time. In addition to those, manufactures will appreciate the smooth rounded surface produced by whirling. Milling cutters produce a pounding action and leave the surface of thread faceted.
At the end of the day, the following things can be said about the thread whirling:
- It produces surfaces finishes similar to grinding
- It delivers better surface integrity than milling
- It is faster than single point threading
- Offers better chip control than single point threading
- Better cycle times on longer threads result
No comments:
Post a Comment